Compact electromagnet
Compact eletromagnet
J. P. Brantut and the of external page Group of Quantum Gases at EPFL has realized an electromagnet combining a large number of windings in a constrained volume with efficient cooling.
Please, check out the external page paper.
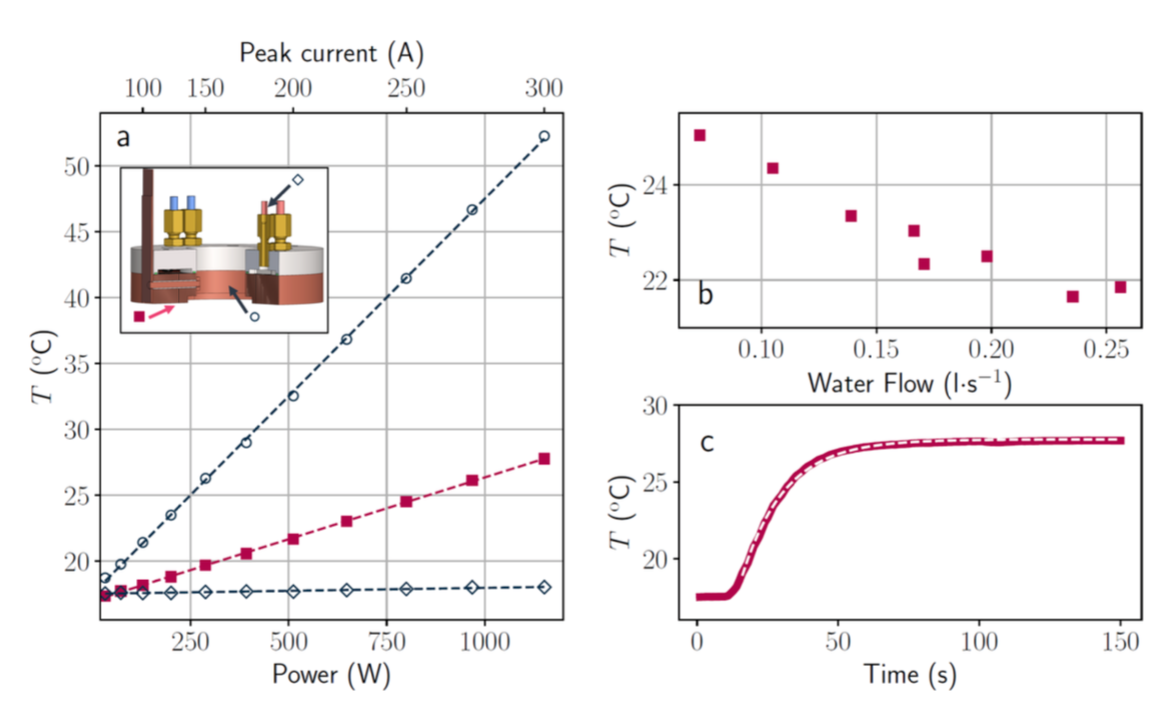
Description
The Laboratory for Quantum Gases at EPFL has developed a new method for manufacturing water-cooled, copper electromagnets with high degree of flexibility, high cooling efficiency and low-pressure water cooling circuit. It is based on a bulk copper plate where a spiral is cut out by wire erosion, and impregnated with epoxy glue. This allows for a wide variety of patterns such as variable pitch and winding diameters. Furthermore, the ensemble forms a rigid body where the current-carrying part can be machined at wish to integrate electrical and water connections. This feature offers high flexibility in the integration of the electromagnet within complex experimental setup. Efficient and homogeneous cooling is achieved by water flowing in direct contact with the upper surface of the the coil.
Key specifications:
winding spacing: 0.38 mm
water cooling pressure: up to 3.5 bars (tested)
winding thickness: < 22 mm (tested)
Further details can be found here (Arxiv link)
Cost of fabrication depends mainly on coil diameter and thickness.
Contact: Kevin Roux (), Prof. Jean-Philippe Brantut ()
More Performance Indicators
An electromagnet combining a large number of windings in a constrained volume with efficient cooling. It is based on bulk copper where a small pitch spiral is cut out and impregnated with epoxy, forming an ensemble which is then machined at will to maximize the use of the available volume. Water cooling is achieved in parallel by direct contact between coolant and the copper windings.
A pair of such coils produces magnetic fields suitable for exploiting the broad Feshbach resonance of 6Li at 832.2 G. It offers a compact and cost-effective solution for quantum gas experiments.
Steady state temperature of the electromagnet as a function of electrical power dissipated with a total coolant flux of 0.23 l·s−1, measured at the inner winding (circles), and bottom surface (squares), and temperature of the water exiting the magnet (diamonds). The dashed lines are linear fit to the data, yielding heating rates of 0.45, 9.4 and 30 K·kW−1 for the water, coil body and inner winding, respectively.
Temperature of the coil body as a function of the total water flux in the coil, for an average electrical power of 512 W.
Time evolution of the temperature of the coil body following a sudden switch-on of 300 A. The thick red line represents measurements and the dashed line is an exponential fit yielding a timescale of 15.26 s.